Plasma cutting is a highly popular, efficient, and precise method for cutting metals and other materials. It involves melting or vaporizing the material with a high-temperature plasma arc to cut through it with ease. A plasma cutting system consists of a plasma power supply, a control unit, and a torch head that creates and directs the plasma arc.
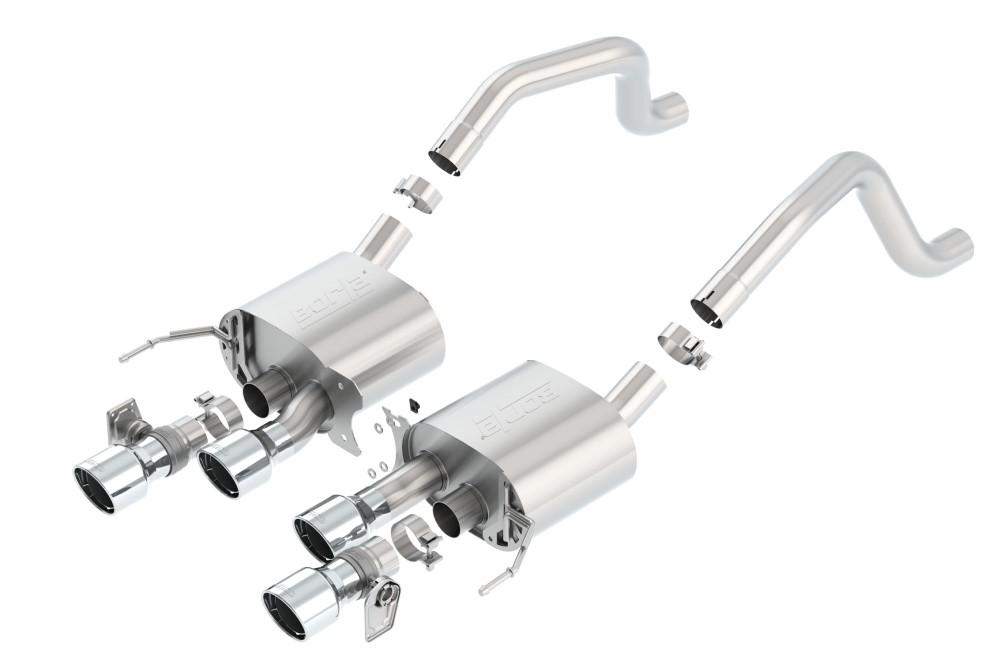
Here, we'll go over everything you need to know about plasma cutting systems, their advantages and disadvantages, and what to consider when investing in one.
Advantages of Plasma Cutting System
1. Speed and Efficiency: Plasma cutting is faster and more efficient than many other cutting methods, such as manual cutting and oxy-fuel cutting. It can cut materials at high speed, reducing the time and cost of production.
2. Precision: Plasma cutting is highly precise and can make intricate cuts and designs with ease. The plasma arc can be focused to produce a small, concentrated heat source, allowing for clean and precise cuts.
3. Versatility: Plasma cutting systems can cut various materials, including mild steel, stainless steel, aluminum, copper, and brass.
4. Clean Cuts: Plasma cutting produces minimal slag, minimizing the need for cleaning and reducing downtime.
5. Reduced Heat Affected Zone: The plasma's high temperature produces a small heat-affected zone (HAZ) that minimizes distortion and warping.
Disadvantages of Plasma Cutting System
1. Initial Cost: Plasma cutting systems can be expensive compared to other cutting methods. However, the long-term savings in time and efficiency can outweigh the initial cost.
2. Limited cutting thickness: Plasma cutting systems have a limited cutting thickness, typically up to 2 inches. Beyond this thickness, other cutting methods may be required.
3. Consumables: Plasma torches require consumable parts, including electrodes, nozzles, and shields, which need periodic replacement, adding to operating costs.
What to Consider When Making an Investment?
1. Cutting Thickness: Determine the maximum thickness of the material you intend to cut and choose a plasma cutting system that can handle it.
2. Speed: Consider the speed you need for your cutting applications and choose a plasma cutting system that meets your speed requirements.
3. Precision: Consider the level of precision required for your cutting needs and choose a plasma cutting system that can deliver that level of precision.
4. Ease of Use: Choose a system that is user-friendly, with easy-to-navigate software and control panels.
5. Cost: When making a purchasing decision, factor in the initial cost, operating costs, and overall value for the system.
Shandong Buluoer Intelligent Technology Co., Ltd. specializes in CNC plasma cutting machines, CNC flame cutting machines, laser cutting equipment, welding equipment, and more. Our plasma cutting systems are of the highest quality, featuring advanced technology and reliable performance. We also offer customized solutions to meet your specific cutting needs.
Conclusion:
Plasma cutting systems are an excellent investment for any metalworking operation. With their speed, precision, versatility, and clean cuts, they can save time and improve efficiency while helping to minimize costs. When choosing a plasma cutting system, consider the cutting thickness, speed, precision, ease of use, and cost to ensure that you invest in the best system for your specific needs.